Our factory has a very advanced and modern production line that is completely dependent on any control from the beginning of production to shipping and loading
Our factory has a very advanced and modern production line that is completely dependent on any control from the beginning of production to shipping and loading
Ballestra’s SULPHUREX film sulphonation technology presents outstanding advantages over the competing processes, namely:
- Excellent performances in terms of product quality, especially when sensible raw materials are processed
- Exceptionally good conversion rate and colour with maximum achievable absorption of SO3 gas Listed below are the main features of the process sections of a Ballestra plant
The atmospheric air is compressed up to 0,7 barg as requested by the downstream sulphonation process.
The compressed air is dried by refrigeration and condensation of the water contained in the atmospheric air and subsequent absorption on a desiccant bed.
- Low operating pressure design (0,7 barg max)
- Process Air Dew Point lower than -70°C
- Fully automatic regeneration of absorbent medium (silica gel)
- Low energy consumption due to the recovery of the hot air from SO3 production unit for absorbent medium regeneration
- High reliability and efficiency
Liquid sulphur is burned with the process air in a special furnace to produce a gas containing 7% by volume of SO2.
The SO2 is then converted to SO3 in a special conversion tower equipped with 4 Vanadium based catalyst beds and intercoolers to optimize kinetically and thermodynamically the reaction yield. The SO3 gas is finally cooled to 50-60°C as requested by the sulphonation process.
- Very high reaction yield : 98,5% guaranteed
- High reliability, safety and long plant lifetime due to the use of air as a cooling medium, instead of water, to minimize corrosion risks
- Special design of sulphur furnace ensuring high operating reliability and easiness
- High energetic efficiency thanks to the use of hot cooling air for silicagel regeneration in the Air Drying Unit
- Very compact design of the conversion tower with internal intercoolers
- Reduced plant start-up time due to a special sulphur furnace which does not require preheating
The SO3 gas outcoming the SO3 production unit is filtered by a special high efficiency brink filter to eliminate any trace of carried-over oleum. Then is fed to the top of the Multitube Falling Film Sulphonation reactor (MTHFR) where also the organic raw material is fed under mass flow control. The reaction of SO3 gas with the organic raw material takes place in the MTHFR.
At the outlet of the reactor the gas/liquid mixture is separated in a special gas/liquid separator and in a downstream gas cyclone. The sulphonic acid is sent to a special ageing/stabilizing unit when Linear Alkylbenzene is processed,
- Product quality meeting the highest international standards
- High operating flexibility and High reliability and operation easiness
- Automatic in-line control of sulphonation degree
- Low energy demand thanks to the low pressure drop of the MTHFR
- Very high heat transfer efficiency that enables an accurate control of the temperature profile in the reactor Which leads to a high quality product
- Low pressure drop (0,3 barg average) resulting in a reduced energy consumption of the whole sulphonation plant
- High reliability and longer lifetime thanks to the use of sophisticated corrosion resistant alloys for critical parts Which leads to the absence of any iron compounds in the product
The exhaust gas exiting the sulphonation reactors is processed to reduce the level of pollutant to values widely accepted by the most stringent international standards on emissions to atmosphere.
The maximum content of the polluting agents guaranteed at plant stack is the following:
- SO2: 5 ppm (vol.)
- SO3: 15 ppm (vol.)
- Organic mist: 25 mg/m3
The exhaust gas undergoes two subsequent steps of treatment before being released to the atmosphere: reduction of organic mist content and final washing with a caustic soda solution to reduce the amount of free SO2 discharged.
This latter step is carried out in a suitable SO2 scrubber, while for the elimination of the organic mist with brink filter (NEGT)
The unit is based on a special Multi cartridge High Efficiency brink filter constantly washed with fresh organic raw material.
allows the complete recovery of the sulphonic acid carried over by the exhaust gas.
As additional advantage, the NEXT system enables the recovery, as finished product, of the organic drippings,
Our industry professionals are able to deliver better ideas and solutions embedded with a deep understanding of each client’ business and industry.
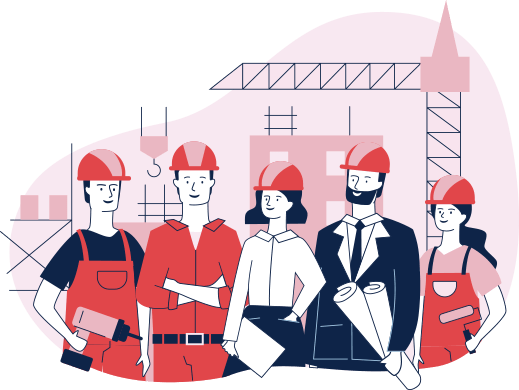